The production of carbon fiber surface felt first requires high-quality carbon fiber and organic rubber powder as raw materials. High-quality carbon fiber should have the characteristics of high strength, high modulus and high conductivity, while the organic rubber powder should have appropriate viscosity and viscosity. When purchasing raw materials, priority should be given to qualified materials provided by regular manufacturers to avoid low-priced and defective products. In addition, raw materials need to be strictly inspected before entering the production line to ensure that they meet production requirements.
2. Pre-impregnation process
Pre-impregnation is an important process step to enhance the strength and hardness of raw felt. During the pre-impregnation process, the original felt is put into the prepreg liquid for impregnation, so that the fiber and resin are in complete contact and solidified, thereby improving the mechanical properties of the carbon felt. Pre-dip fluid is generally composed of resin, solvent and curing agent. Resins with different properties can be selected according to different application requirements. During the pre-impregnation process, parameters such as the concentration, temperature and impregnation time of the prepreg solution need to be controlled to ensure full contact and solidification of the fiber and resin.
3. Hot pressing process
The hot pressing process mainly relies on the effects of heat and pressure. Under high temperature conditions, the thermal motion of the molecules of the material intensifies and the distance between the molecules increases, which is conducive to the mutual diffusion and combination of molecules. At the same time, the effect of pressure makes the contact between materials closer, which is conducive to the interaction and bonding of molecules. This combined effect of heat and pressure causes physical or chemical changes in the material during the hot pressing process, thereby achieving the desired processing effect. The hot pressing process is widely used in the processing and joining of various materials, such as plastic, rubber, wood, fiberboard, metal, etc. In plastic processing, the hot pressing process is often used to make plastic sheets, pipes, special profiles, etc.; in wood processing, the hot pressing process is often used to make fiberboards, particleboards, etc.; in metal processing, the hot pressing process is often used to make metal powder metallurgy. products, etc.
4. Carbonization process
Carbonization is a process in which the pre-pressed and cured felt layer is treated at high temperature to carbonize the resin and form carbon fibers. During the carbonization process, it is necessary to control the carbonization temperature and holding time, as well as atmosphere control, to ensure that the fibers are completely carbonized and form high-quality carbon fibers. The selection of carbonization temperature should be determined according to the requirements of raw materials and products, generally above 1000°C. The length of heat preservation time will also affect the carbonization effect and needs to be adjusted according to the actual situation. In addition, attention needs to be paid to the control of the atmosphere during the carbonization process to avoid the impact of impurities such as oxygen on carbonization.
5. Surface treatment process
Surface treatment process refers to a process that changes the properties and appearance of the material surface through physical, chemical or mechanical treatment of the material surface. It can make the material surface have certain functionality and decoration, and improve the service life and adhesion of the material. There are three processing methods:
Physical treatment: Physical treatment mainly changes the properties of the material surface through physical methods, such as sandblasting, shot peening, polishing, micro-arc oxidation, etc. These methods can change the roughness, smoothness, hardness and wear resistance of the material surface.
Chemical treatment: Chemical treatment uses chemical reactions to change the properties of the material surface, such as electroplating, anodizing, chemical oxidation, coloring conversion coating, etc. These methods can form a layer of compounds or alloys on the surface of the material that is different from the base material, thereby improving the corrosion resistance, decoration and conductivity of the material.
Mechanical treatment: Mechanical treatment uses mechanical force to change the shape and properties of the material surface, such as grinding, cutting, rolling, etc. These methods can make the material surface flatter and smoother, and eliminate surface defects and burrs.
6. Quality control and testing
In the production process of carbon fiber surface felt, quality control and testing are crucial links. All aspects of the production process need to be strictly monitored and tested to ensure that the products meet quality requirements. Common testing methods include tensile strength testing, conductivity testing, density testing, etc. At the same time, abnormal situations in the production process also need to be handled and recorded in a timely manner for subsequent analysis and improvement.
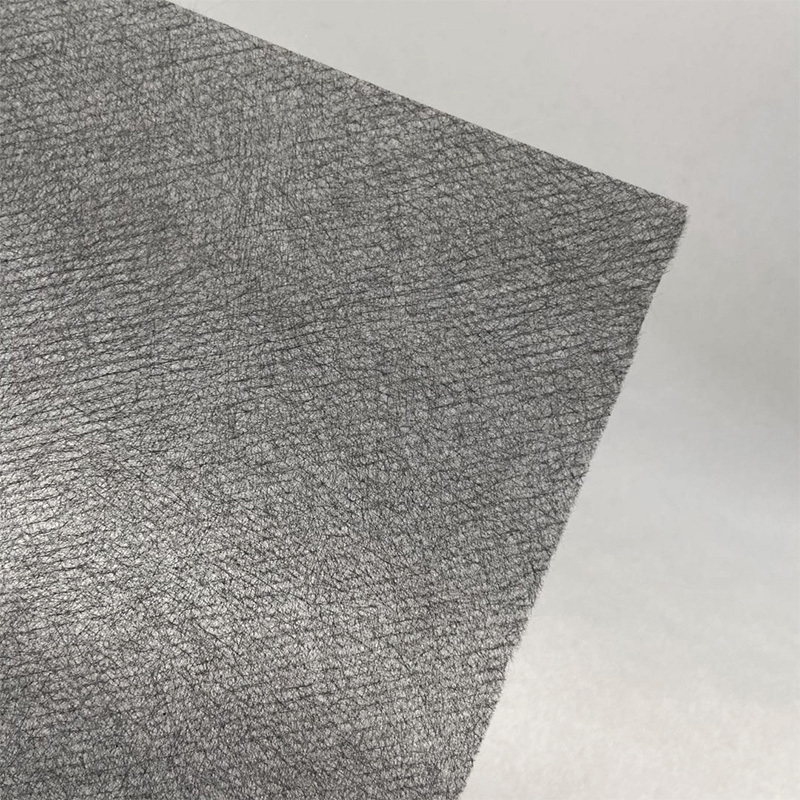